The Standard Carburettor fitted to 350 and 500 Royal Enfield India Bullets is a Mikcarb, a copy, made under licence, of the popular Japanese Mikuni. The 350 Bullet uses a flange-mounted 24mm bore version and the 500 Bullet uses a 28mmbore, mounted
on a rubber stub. The other details are similar for both.
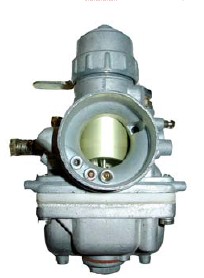
Before blaming the carburettor for poor performance, hard starting, back-firing etc. a few simple checks should be done. Engines need a supply of clean, fresh petrol. Pull the fuel supply pipe off the carb, turn on the fuel tap and run off a small amount of petrol into a clean glass jar. Stale petrol has an unmistakable smell; rust or water will quickly settle to the bottom of the jar.
A common fault is an air leak due to a perished intake rubber or over-tightened flange. Leaks will cause the exhaust to smoke and engine speed to rise.
Next stage is to check on the ignition. After a short run, remove the plug and check the colour and condition of the tip. A sooty plug shows an over-rich mixture, a ‘hot’ nearly white plug tip shows a weak mixture and a hot running engine.
The firing-ends shown in the photograph above are all considered ‘good’ by NGK technicians.
Our experience is that on Bullets ideally the plug tip should be slightly sooty, indicating a slightly rich mixture.
Now test the spark, which should be blue, snappy and strong. A low battery, dirty or worn points or a weak condenser will all give a weak, yellow spark and produce similar symptoms to carburetion problems. A new spark plug (short reach for a 350, long reach for the 500) might be all you need. When fitting the spark plug, lightly smear the threads with copper grease, replace the plug with your fingers, screwing in the plug with your fingers until it is ‘seated’, tighten no more than a quarter turn with a plug spanner. Take care not to over-tighten the plug—overtightening spark plugs is a common cause of thread damage, which can be costly to repair.
If none of these steps cure your bike’s problems then turn off the fuel, and unscrew the carb top from the body. Carefully lift out the slide.
Remove the carb — but beware as petrol will spill from the float chamber, so be certain that there is nothing to cause a fire. Working on a clean surface, turn the carb over and remove the four screws which hold the float bowl.
Ease the float bowl away from the main carb body (a quick tap with the handle of your
screwdriver will release the gasket’s hold). Tap the float spindle out, lift the float assembly away and tip the float needle out. Check the float for leaks – a quick shake will show if there is petrol inside the float. Clean the float needle with a spray of carb cleaner. The spring-loaded plunger must be free moving. Replace the float needle, float assembly and spindle. With the carb held upside down and the float chamber gasket removed measure from the carb body surface to the top of the float, as shown below. The standard measurement is between 24-26mm (see picture).
If necessary the float height can be adjusted by gently bending the tangs located between the two brass floats.
With the float bowl removed the jets will be seen in the centre of the carburettor (see the picture below). Now is the time to remove the pilot and main jets, to clean them, check their sizes or change them.
With a suitable screwdriver carefully unscrew and remove the main jet with its washer – the washer may need to be carefully prised out of its housing. The main jet screws into the base of the needle jet. The needle jet cannot be removed from this end of the carb.
To remove the needle jet, detach the carb top and remove slide, unscrew the main jet (as just described) and tap the needle jet up into the carb body. Refitting is the reverse of this procedure. Be careful on refitting that the slot in the bottom end of the needle jet locates in the spigot in the base of the jet housing (see picture below) – it may help to use long-nose pliers. Take care not to cross-thread the main jet in the needle jet and don’t over-tighten.
NOTE: In certain cases the needle jet may not screw fully into the main jet. There are two types of jets, each with a different thread pattern, to prevent a jet of one type being substituted for a jet of the other type.
The pilot jet is the small jet located in the deep drilling next to the main jet (see the picture). To remove the pilot jet unscrew it carefully with an appropriate flat blade screwdriver and gently shake it out of its housing.
If you have made changes to the air filter or exhaust system now is the time to fit new jets. Different air filters or silencers affect the amount of air the engine is able to ‘breathe’. As more air is drawn into the engine the ratio of petrol to air decreases, the result is a mixture weaker than the ideal of about 14 parts air to 1 part petrol. If the mixture is too weak the engine performance will be adversely affected—the engine may over-heat, with potentially serious damage to crucial engine components. The remedy may be to adjust the air screw and/or move the throttle needle clip but in most cases it will be necessary to replace the jets—the higher numbered jets let more petrol into the carburettor, giving a richer mixture.
There are three jets in the Mikcarb: the pilot jet (used at small throttle openings), the needle jet (used at throttle openings of about ¼ to ¾ – this jet is only available in a standard size for 350 engines) and the main jet (used from ¾ to full throttle).
The mixture at small throttle openings is also affected by the size of the cutaway in the throttle slide. The larger the cutaway (the higher the throttle slide number) the weaker the mixture, as more air is allowed into the carburettor. A smaller cutaway will, of course, give a richer mixture.
Fine adjustment to the mid-range may be made by raising or lowering the throttle needle. Release the throttle cable from the alloy block inside the slide. There is a small plate that
prevents the cable from accidentally detaching itself from the slide, note how the tag and slots are fitted. (The picture below illustrates the method used for fitting the throttle cable.) Unscrew the two screws, lift out the block and the needle will drop out. By refitting the clip in a lower groove you will richen the mixture (this raises the needle and so allows more fuel through the needle jet). Placing the clip in a higher groove weakens the mixture.
When reassembling be sure the slide locates in the peg projecting from the side of the carb (see the picture below). Take care that the throttle cable is routed without sharp kinks and has enough free-play for the slide to drop fully – even on full lock with the petrol tank in place. Replace the fuel pipe and check for leaks.
Setting the tick-over requires patient sequential adjustment of the pilot air screw and the throttle stop screw (see picture below). Turn the pilot air screw fully in and then out one and a half complete turns. Start the engine and allow it to warm-up thoroughly. When the engine will run cleanly without the enrichment of the mixture provided by the use of the cold start plunger, close the starting jet by lifting the cold starter lever to its horizontal position.
• Adjust the throttle stop screw so the engine runs at a fast tick-over, say about 20%
above the idle speed you wish to achieve
• Unscrew the pilot air screw to increase the engine speed to its fastest possible
• Gradually unscrew the throttle stop screw to reduce engine speed to the target idle
speed
• Again unscrew the pilot air screw to increase engine to the highest tick-over possible
• Finally, gradually unscrew the throttle stop screw to reduce engine speed to the correct idle speed. (Usually this process carried out twice – as described – will be sufficient to achieve a correct tick-over.)